An Apple a Day Keeps the Doctor Away…
How a brother duo created a bustling team building boards for a better tomorrow. All out of an apple orchard.
By Kailani Wetherell for Sustainable Surf, 29 May 2024.
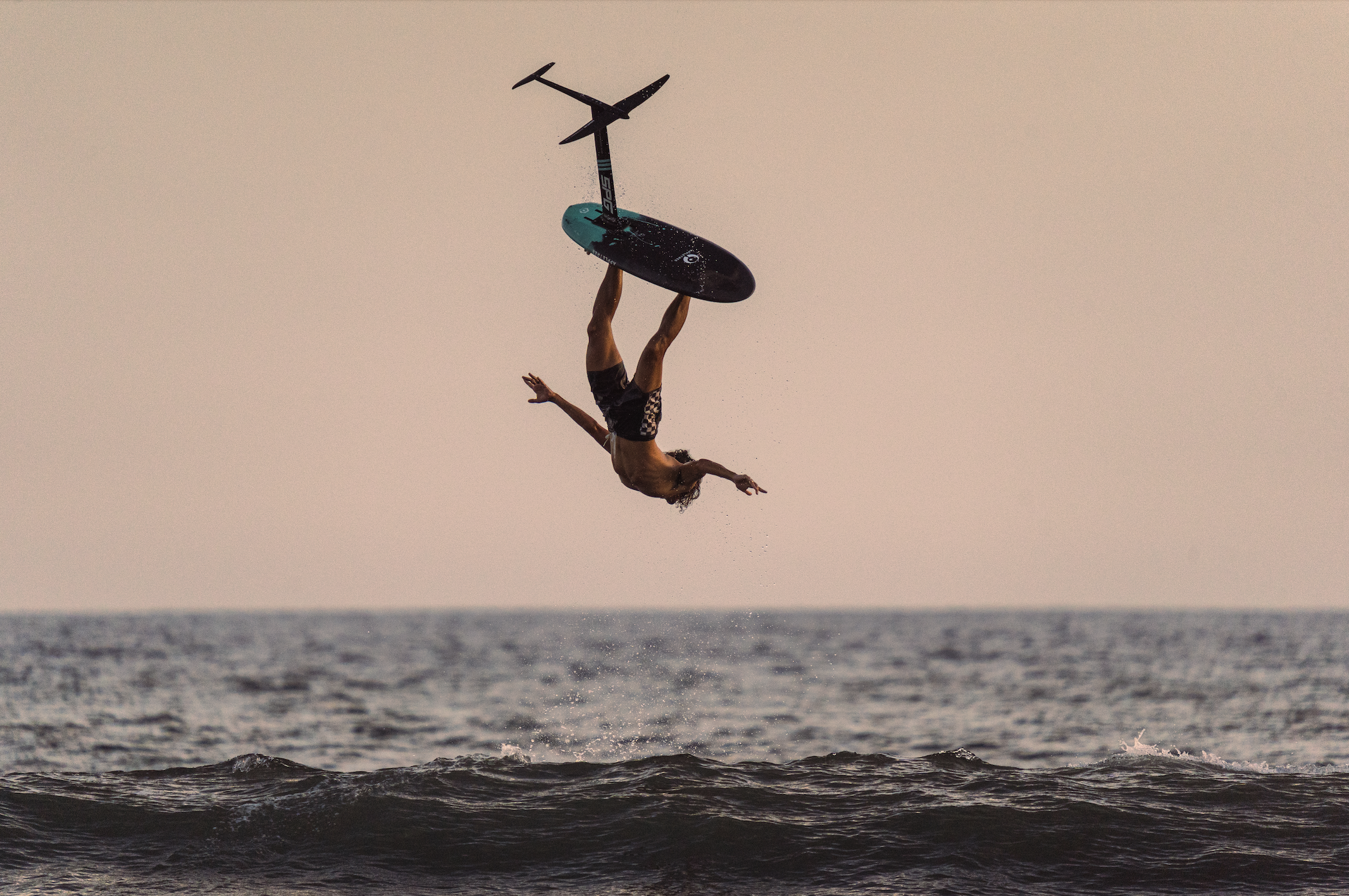
They say an apple a day keeps the doctor away…and with Appletree boards, you’re riding sustainably each day… With roots nestled in the heart of Lisserbroek, a town in the Western Netherlands, Appletree Surfboards began thanks to brother duo Wieger and Jorrit’s who started building in a simple shed on their parents’ apple orchard back in 2006. Founded by the dynamic brothers, Appletree Surfboards was born out of a love for the ocean and a drive to create boards that could withstand the forces of nature while delivering top-notch performance.
HOW DID YOU GUYS START/WHAT’S THE ORIGIN STORY?
It all started in 2006, in our parents’ backyard at an apple orchard in the Netherlands. In a small shed we made our first surfboards. Shaping surfboards was not an obvious choice. To get to the sea we had to ride our bicycles for an hour with a surfboard under our arm. At that time there were no apps or webcams that made accurate weather forecasts. We often cycled for two hours for nothing. But the passion and stoke was big and we kept trying! The first boards we made we mostly used ourselves. Soon others showed interest, which encouraged us to do even better. Plus at that time, kitesurfing was getting bigger and bigger. We kitesurfed on normal surfboards, made in the traditional way. Those boards could not withstand the forces of kitesurfing, so one board after another snapped, bockeld or had such big heel dents that it became unrideable. We were committed to making boards that were a lot more durable, while maintaining performance. After a lot of testing and failed constructions, it was in the year 2014 when we could say with certainty that we had developed a product and technology that was completely unique in the surfing world.
Over the years, the shed has been exchanged for a decent factory in Rijswijk, the Netherlands. In 2019 we had grown out of that too, so we moved to Portugal to build a new factory. It was quite an exciting step for us. Doing business in another country, building a new factory, continuing growth, building a new team, etc. Quite some changes in a short period of time. However, growth continued even faster than we could have ever imagined. After three years we also grew out of that factory. That was the moment we decided to buy a building instead of lease, To build a factory exactly as we wanted. The current factory is 8 times bigger than the previous one: 3500 square meters. Over the years we became a close-knit team of passionate craftsmen and women from different nationalities that we are today. It is the Appletree crew that gave us the confidence to take this next step.
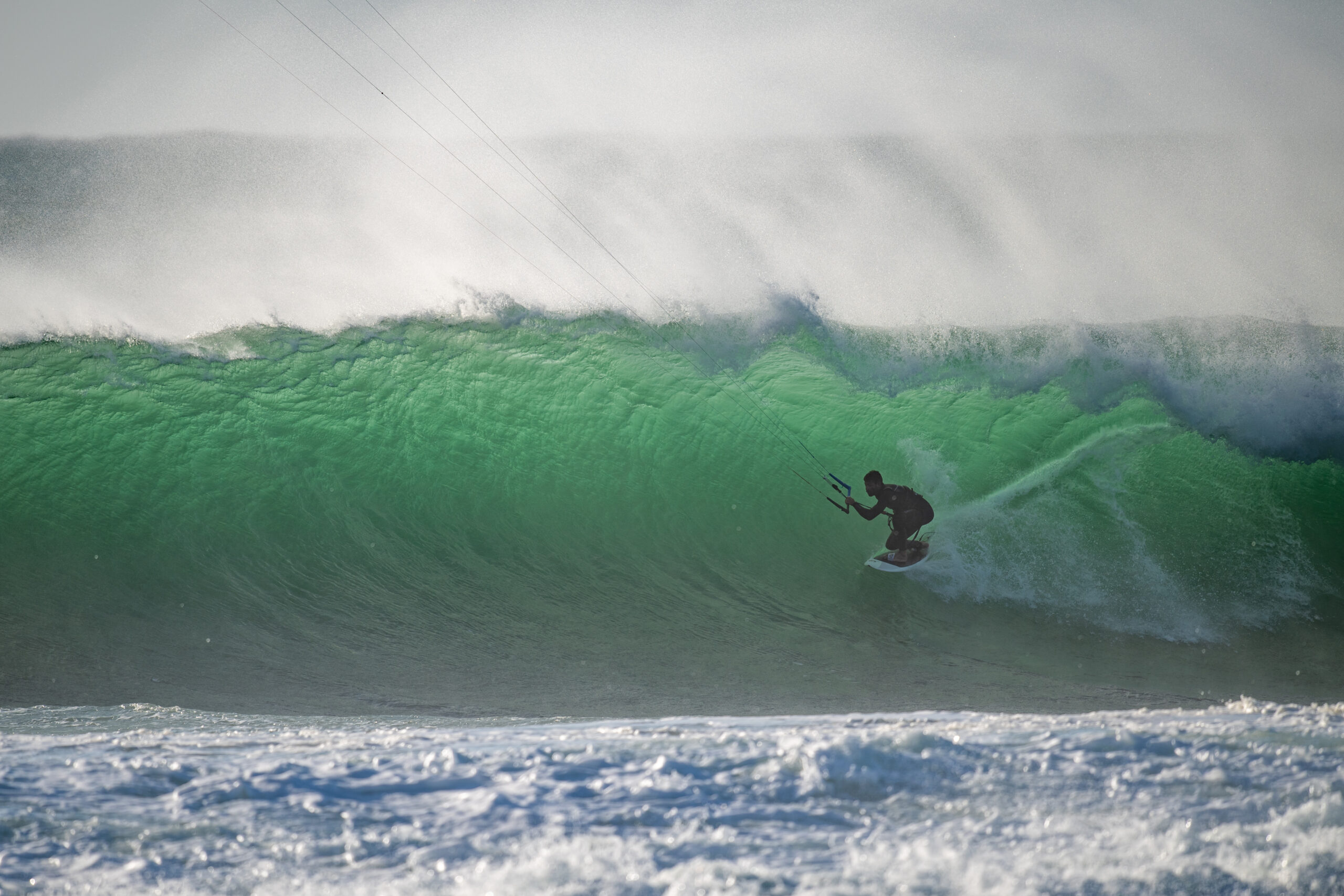
IS THIS A PASSION PROJECT?
Yes, you could say that! In more ways than one. Not only because of our passion for water sports and the outdoors, but also because of our drive to find out how things are made and passion for artisan hand work. With roots deeply embedded in the orchard, our ethos reflects the values instilled by our parents – hard work, determination, drive, innovation, and a deep connection to nature. Our unique construction was not developed overnight. It took us a lot of time, blood sweat and tears. We worked overtime in other jobs to fund this trial and error phase. Without passion, we could not have pursued it.

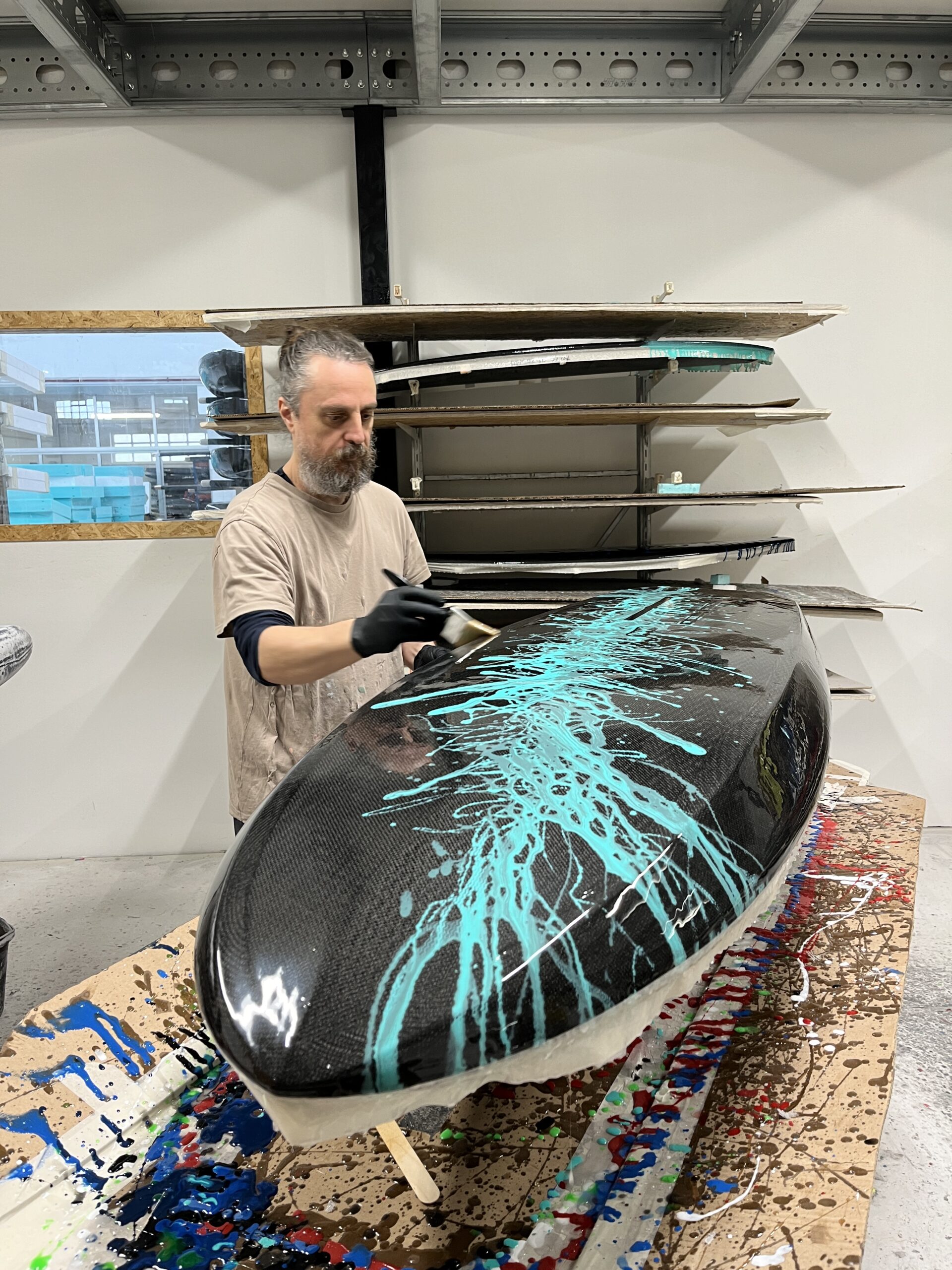
WHY ECO-FRIENDLY BOARDS AND HOW ARE YOU CREATING THEM?
This has never really been a choice for us, but more a matter of course, because it is the right thing to do.
To be honest, we don’t think we can call our boards eco-friendly boards. Even though we have already accomplished a lot in the field of sustainability in recent years, we also still have a long way to go. What we all agree on is that we are not just going to implement the low-hanging fruit, but look at the entire value chain and what we can do to not only minimise our environmental impact, but also provide a good, healthy and inspiring work environment. We are exploring/discussing all areas, from new production techniques or materials to new future proof business models. It should not be the case that we achieve a small sustainable win in one area but pollute more in another. It is important that it is underpinned strategically. There are a number of things we already do in our production process that ensure less impact on the environment. To begin with, the main attribute Appletree boards have is longevity because of our unique production technique. In our opinion, this is one of the most responsible ways of producing. In addition, the vacuum infusion technique we use allows us to better calculate the ratio of resin to fibers, which means we can use less resin and fibers and actually produce a stronger board. Plus, we use 40% bio-based resin in 100% of the boards. Our factory had always had an energy contract with a company that stated that all their electricity was ‘green’. However, our dream was to run the entire factory on renewable energy. Since December 2023, that has become a reality as we invested in solar panels on our factory roof. In general, the sun in Portugal produces more energy than we actually use. So we can also use the access for charging our electric vehicles. An advantage of working primarily with European suppliers is that we are in close contact with most of them and have been able to have discussions about their and our Environment, Social, Governance (ESG) policies and how we can support each other in these respects. One of the agreements we are most happy with, as we know a lot of shapers struggle with this, is the agreement with our foam supplier. We return all leftover foam, such as cut-offs from the CNC machine but even dust from the shaping bay, to our foam supplier, who then recycles it right back into new foam with no loss of quality.
To make this happen, we purchased a compactor that compresses all foam waste into compact packages. This was quite an investment, but a logical choice for us, as we prefer to close as many loops as possible in our production process. Just as we want our boards to have longevity, we want the same from our factory machinery. All our factory machinery and equipment is of high quality and easily repairable. In most cases, we can carry out the repairs ourselves and in others we work with specialized companies. With the safety and health of the employees in the factory being paramount. For cleaning machinery or components and filtering the air, we partner with a specialized company that works according to the most strict environmental and health requirements and also has the same philosophy about equipment lasting as long as possible. What is truly special is that there is a sustainable mindset among the entire Appletree team. The team culture is such that we hold each other accountable for missteps, motivate each other to do better and come up with innovative ideas. One example is that the factory is very strict about separating waste so that we hand it in properly for recycling. But there are plenty of other examples. From our Administrative Assistant looking at a water bill and thinking we should be able to use less water and coming up with ways to make this happen to the quality team coming up with the concept of “leftover pads” from cut offs of deck pads that also work just fine.
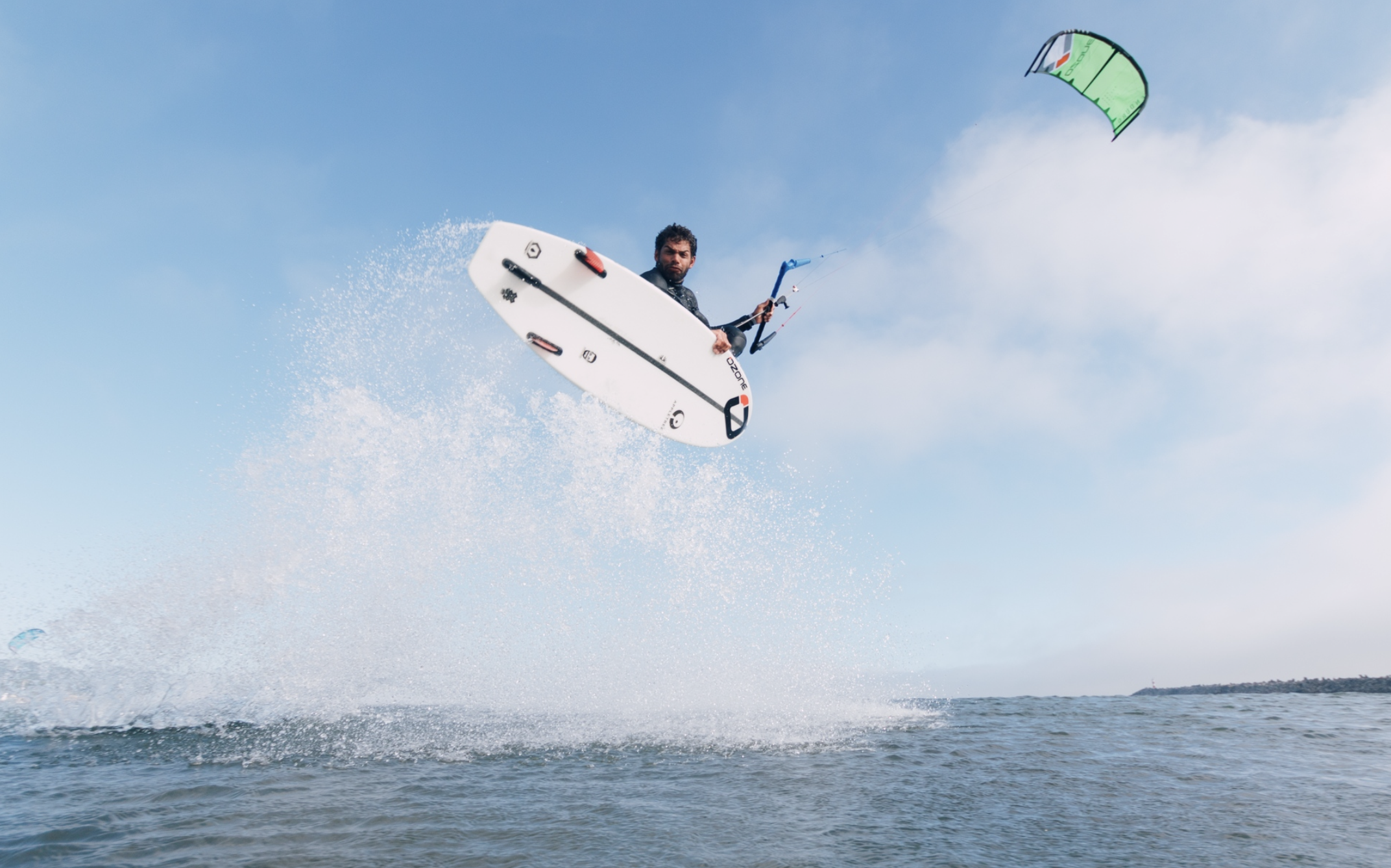
DESCRIBE YOUR APPROACH TO BUILDING/SHAPING ECO-FRIENDLY BOARDS.
Manufacturing long lasting boards. The longer a board is in use, the less impact it has on the environment. Our product design is based on the principles of Ecodesign, pillar of the circular economy. One of the first principles is to already reflect at the product design stage whether the product and or material is really needed. That can go as far as coming up with a new business model for boards, such as PAAS, for example. Which, by the way, we are exploring. But for now, we’re mainly looking at whether something really ensures an improvement, solves an issue or is a well-reasoned addition. This is one of the reasons why we decided not to produce seasonal products. Which in many cases simply means a new colour or minimal change that has no other added value, but does encourage people to buy more. We don’t support that. Another important principle of Ecodesign is the durability/repairability of the product. That’s something we have pushed hard on by developing our unique manufacturing technique that ensures the boards are much more durable than average production boards. Plus our waterproof foam ensures that a ding does not need to be repaired straight away, as the foam does not absorb water. In the end, of course, we do recommend a repair, and that is easy to fix in most cases too, especially if you consult our repair videos. Which are also part of making the boards last even longer. Efficient use of energy and resources is also an important one for us. We looked at how we could keep our energy consumption as low as possible, including energy-efficient machines, but also to source as many materials as possible from Europe, in which we are now about 95% successful. And as mentioned earlier, we’ve invested in solar panels for the factory so that the energy we do use is renewable.
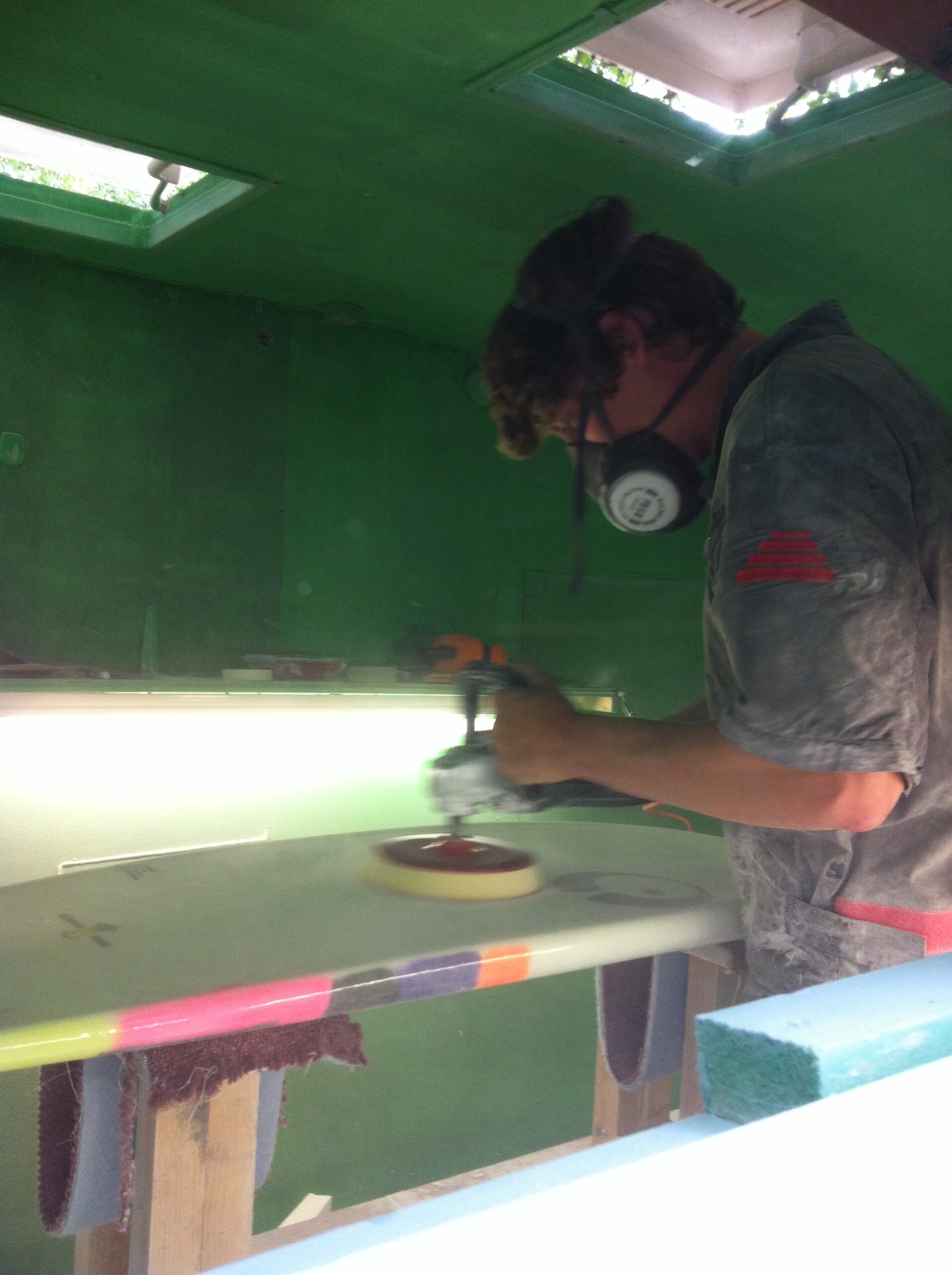
HOW DID YOU COME ACROSS THE ECO-BOARD PROJECT/HOW HAS BEING PART OF IT HELPED YOU?
We were introduced to the Ecoboard project through one of our OEM partners we had at the time, Ben Wilson Surf (BWS). We were excited about it from the beginning and were keen to meet the standards. Above all, it helps us to keep improving on sustainability. It is inspiring to be part of a community that all have the same goal in mind: making the surf industry more sustainable. It also introduces a very valuable network. We have already had several cool collaborations through the Ecoboard Project. In addition, Sustainable Surf has a wealth of information material that helps us substantiate our sustainability goals. For example, the Life Cycle Assessment (LCA) of a traditional and an ecoboard. It clarified for us what we needed to invest in first in terms of sustainability. In addition, it has also motivated us to conduct our own LCA, for which we are now collecting data. What we hope is that we can serve as an example of how you can also produce Ecoboards on a larger scale, as long as you design your production process accordingly and keep innovating. We are now working with several OEM partners who have chosen to have boards produced by Appletree instead of at factories that do not take sustainability (in the broadest sense of the word) as seriously. It helps us to make an impact on a larger scale. We are pleased that other brands, which may not have their own factory, do make a conscious decision to partner with a factory that values sustainability. Like when Appletree was just starting out, this encourages us to do even better. Plus also don’t underestimate how much (innovative) knowledge our OEM partners share with us. It’s great to see that we are working together towards a higher goal and don’t consider each other as competitors in this.
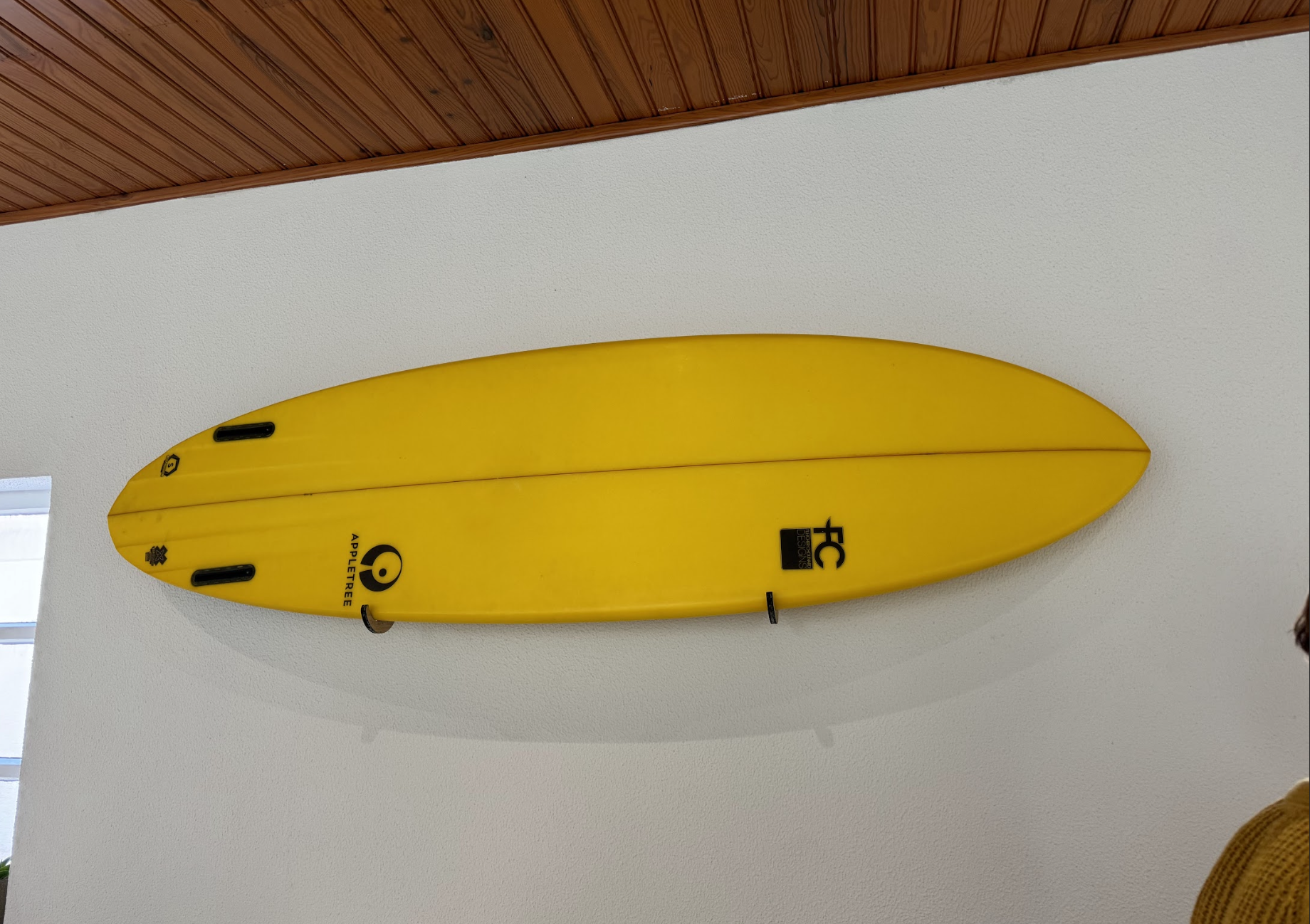
WHAT DO YOU HOPE TO DO IN THE FUTURE WITH THESE BOARDS?
Oh we still have so many more plans for our boards. We are far from finished innovating! The thing at the top of our list is performing LCAs for both our glass and carbon boards. We want to be able to better substantiate where we can make the biggest wins in terms of sustainability. So that we can target our focus, money and time. We also want to add the data to the digital passport of our boards. Every Appletree board already has a digital passport, using an NFC tag, but it still only holds limited information. By sharing our LCA data, we want to create more transparency for clients who want to buy or already own an Appletree board.
Another thing we have been exploring for a while is using more sustainable materials. For this, we are in talks with several partners. However, we do not want it to come at the expense of the boards’ durability. So it will take quite some research before we can say whether it is a good solution and actually implement it.
WHO DO YOU HOPE THIS INSPIRES?
We hope this inspires everyone looking to buy a new board, to think about the consequences of our actions and make a conscious choice. That standard (cheap) PU/poly board might look like a good deal at first. But if you take a look at the whole production process and lifetime of the board, is it really such a good deal? We also hope to help reach out to and inspire other board builders, together with sustainable surf. Sustainability only works if it’s in your every move, and not just a cool/hip trend that you want to join. You have to consider it in every move, everything you buy and consume and every (business) decision you make. Even if it’s not always the easy choice.
Curious to know what’s in the works? Follow their team and all of their creative endeavors on Instagram @appletreesurfboards.