After the Wax: The Rise of Beeswax Glassing in Surfboard Construction
A follow up interview with ECOBOARD Program Manager Tyler Fox and surfer and shaper, Charlie Cadin.
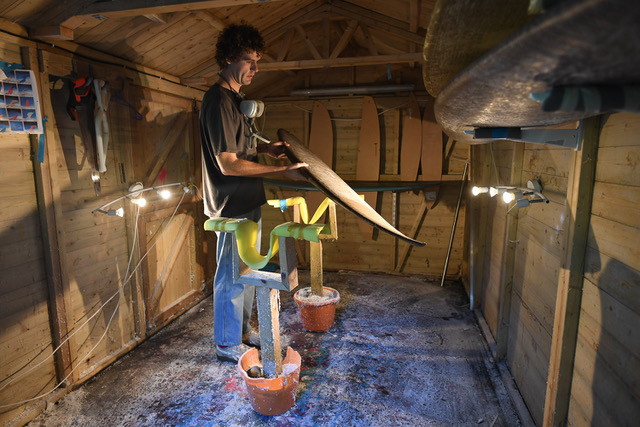
Tyler: Congratulations Charlie this is quite a breakthrough! From what you’ve explained to me about this new process of coating surfboards using only Beeswax it sounds like it has some huge potential to really make a difference in the toxicity of surfboards and the production process. Can you explain how the heck you came up with this idea?
Charlie: Thank you! I was looking at resins, as they have kind of been untouchable in terms of the last element of a board which has remained challenging to reduce the toxicity. Resins are basically thermosetting plastics, meaning they harden once and then can’t be melted. I started thinking about thermoforming plastics, like plastic bottles, which can be melted again and again, and then came across beeswax. It can be remelted again and again, and is completely bio based.
Tyler: You had mentioned that instead of trying to patent your process or formula you’d rather just see more small board builders creating boards safer without the toxicity. Explain how someone can actually build a board this way? The materials they’d need etc.
Charlie: The plan with the video was to make it a bit like a recipe, with all the steps needed. Once the board is shaped all you have to do is choose and cut your reinforcement fabric, and melt and drip beeswax over the cloth. Cover about 1/3rd of the board, and then using a heat gun or hair dryer and a spreader, spread the wax over the cloth. there’s no rush as you can just remelt the hardened resin.
Tyler: The core of your first proper prototype you used a standard PU blank… Have you tried and or thought about using other cores for upcoming boards so that they could be truly biodegradable?
Charlie: The core was PU to provide a constant really, so that it could be directly comparable to resins. it would be cool to experiment with the Polyola foam, or alternatively a wood or agave core to make it a fully biodegradable surfboard.
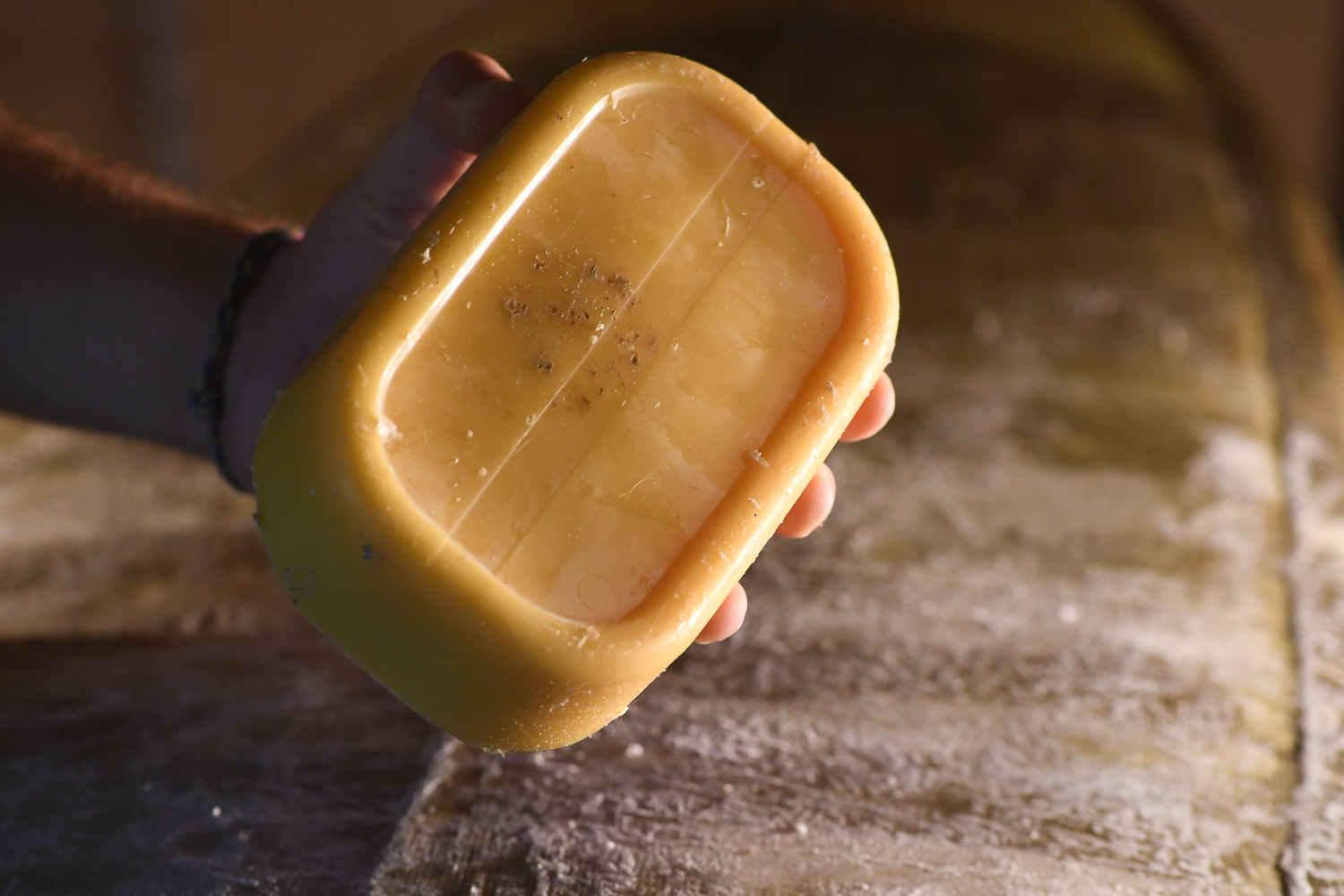
Tyler: How much stress testing have you guys done? How do you know if boards constructed this way will hold up in powerful overhead surf?
Charlie: There is only one way to find out really! I have made a few boards now , and they hold up really well. It is interesting to play around with different fabric layups, and as the beeswax is so light and only needs a single coat, multiple layers of cloth can be used without causing weight issues.
Tyler: Do you see any drawbacks of this process in regards to mass adoption? Higher costs to construct? Time constraints?
Charlie: It actually wins in both of those categories as there is no drying time, boards can be glassed in a couple hours instead of days. Resin costs about $30 per surfboard, whereas beeswax is much cheaper- speak to your local beekeeper. As with most bio-based materials the real test comes with time, and durability in the long run.
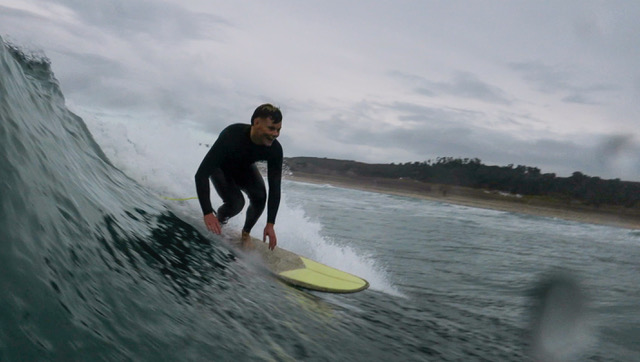
Tyler: I, for one, would love to see and or test a board constructed this way… How can people get their hands or feet on one of these boards?
Charlie: Give it a go yourself! As there are no harmful fumes produced, you could literally glass a board in your bedroom. if you find a wood core you can shape outside, and glass outside with the beeswax too if you’re short on space. It’s quite cool that the beeswax can make it more accessible for people to try shaping and glassing themselves.
Stay updated on all things shaping by following Charlie Cadin on Instagram @Charlie.cadin.